In recent years, the mining industry has undergone a transformation with the rise of autonomous
mining trucks and robots, replacing traditional manual methods. The global mining truck market
is experiencing notable growth, with its size expected to increase from USD 25.2 billion in 2024
to USD 35.1 billion by 2033, reflecting a CAGR of 3.74% from 2025 to 2033. Several factors are
driving this expansion: Gordon Barratt of Mining & Quarry World looks at the evolving demands
of mining operations via the use of Haul Trucks and Automation.
1.The rise in deep-sea mining and offshore exploration activities has led to increased demand for specialized mining trucks capable of operating in challenging and remote environments. These sectors require heavy-duty trucks designed for robust performance in harsh conditions, contributing to the market’s growth.
2.There is a growing trend of partnerships between mining companies and truck manufacturers to develop customized, efficient, and tailored solutions. These collaborations focus on improving the performance, safety, and reliability of mining trucks, ensuring they meet the evolving demands of modern mining operations.
3.Key Market Trends:
- Technological Advancements: Increasing automation and integration of AI, IoT, and GPS technologies to improve fleet management and operational efficiency.
- Energy-Efficient Models: The development of trucks with lower fuel consumption or electric alternatives to meet sustainability goals.
- Demand from Emerging Markets: As mining activities expand in regions like Africa and Latin America, there is a growing demand for mining trucks suited to different terrains and mining practices.
The mining truck is a colossal vehicle designed to transport heavy loads of mined materials from excavation sites. Towering in size, these trucks can carry hundreds of tons of minerals, ores, or coal in a single haul. Engineered for extreme conditions, they boast robust frames, powerful engines, and durable tires, enabling them to navigate rugged terrain and steep inclines easily. Advanced safety features and autonomous technologies have revolutionized the sector, thus enhancing productivity and minimizing human risk. The product contributes significantly to the efficiency of large-scale mining operations, ensuring the steady flow of resources and bolstering the foundations of modern industries worldwide.
The increasing integration of real-time monitoring and data analytics is fostering the market. Mining companies are leveraging advanced sensors and telematics systems to gather real-time critical data from the product. These sensors track fuel consumption, engine health, tire pressure, load capacity, and operating conditions. The data collected is then transmitted to centralized systems where sophisticated data analytics tools process and analyse it. By harnessing the power of data analytics, mining operators can identify inefficiencies, track equipment health, and make informed decisions to enhance overall productivity. Predictive maintenance models can anticipate potential breakdowns and schedule maintenance proactively, minimizing downtime and increasing equipment availability. Furthermore, real-time monitoring aids in optimizing truck routing, enabling better load balancing and fuel efficiency. The integration of real-time monitoring and data analytics streamlines mining operations and enhances safety by providing insights into driver behaviour and potential risks. This is revolutionizing the mining industry, driving cost savings, improved resource utilization, and sustainable mining practices.
I was impressed by the technological advancements showcased at MINExpo 2024 in Las Vegas. The event highlighted the crucial partnerships between mining companies and heavy equipment manufacturers like Caterpillar, Liebherr and Komatsu all striving for a sustainable future. These collaborations are key to achieving the industry’s net-zero emissions target by 2050. The focus on technology, particularly on carbon emission reduction, driven by the shared goal of achieving net-zero operations by 2050, mining companies are collaborating with heavy equipment manufacturers. My attendance at MINExpo, with its impressive display of equipment and machinery, reinforced my belief in the power of technology to achieve these sustainability targets. The following content highlights some of the key areas of progression from some of our leading mining manufacturers:
Caterpillar affirms large mining truck product line commitment through the energy transition
Caterpillar is reinforcing its commitment to deliver product design choices in alignment with customers’ operational, sustainability and productivity goals that increase the value of a machine throughout its lifetime. These designs align with Caterpillar’s strategy to deliver integrated site solutions to support customers today and through the energy transition.
As the industry looks to the future, Caterpillar is purposefully designing a modular Cat® 793 large mining truck platform with powertrain flexibility. This platform will include diesel mechanical, diesel electric and battery electric options.
Additionally, Caterpillar is leveraging the knowledge and validation acquired through its Early Learner battery electric large mining truck program to drive common platform benefits for its ultra class trucks, including diesel electric and battery electric offerings for the Cat 794, 796 and 798 models.
Caterpillar has a legacy of designing products with ‘customers’ current and future needs in mind. For decades, Caterpillar and the Cat dealer network have provided flexible solutions to extend the life of mining trucks, including retrofit kits, update and upgrade programs and full machine rebuilds. These options can extend a customer’s equipment to align with current products and technologies while reducing total cost of ownership.
Caterpillar Group President Denise Johnson quoted, “No matter the powertrain you desire, we will have a solution. Designing and supporting machine platforms that drive commonality, modularity and a seamless experience across our product lines is not new to us. Our large mining trucks are engineered to integrate with the technologies of today and of the future.”
All current diesel electric and battery electric large mining truck platforms are also compatible with the recently announced Cat Dynamic Energy Transfer system, providing immediate benefit to mine sites that want to lower their operating costs and greenhouse gas emissions while providing flexibility for the future.
Caterpillar Senior Vice President Greg Hepler said, “Caterpillar recognizes every mine site requires a unique plan to meet their sustainability objectives, which is why we are delivering a suite of integrated energy transition solutions, including machines with powertrain flexibility, energy transfer systems, energy storage and management capabilities, autonomy, and fleet management systems. Together with our Cat dealers, we are committed to supporting customers through every step of their energy transition journeys.”
Cat® MineStar™ Command for hauling manages the autonomous ecosystem to increase haulage efficiency, enhance safety
Caterpillar’s continuous investment and innovation in autonomous haulage with Cat® MineStar™ Command for hauling has resulted in hundreds of trucks operating at dozens of sites across three continents. Offering multiple layers of protection to enhance safety at the mine site, the Caterpillar autonomous haulage solution drives hauling consistency and predictability at operations to enhance productivity and reduce cost.
Leveraging decades of development and more than 11 years of operational experience, trucks equipped with Command for hauling surpassed 8.3 billion tons (9.1 billion tons) of material autonomously hauled as of September 2024. MineStar Command manages the autonomous ecosystem to increase haulage efficiency through less idle time, bunching at the loader, unnecessary empty travel and wasted fuel.
“Caterpillar stands at the forefront of autonomous technology for a reason. They consistently advocate for a well-rounded solution that delivers and showcases value in safety, productivity, and efficiency. “We are constantly striving for excellence and innovation. We understand that achieving long-term sustainability requires a united focus on people, processes, and technology.”
Cat autonomous technology is key to enhancing mine site safety. Command for hauling enhances safety by removing haul truck operators from potentially hazardous conditions. Cat autonomous trucks can detect and react to surrounding conditions and obstacles as well as interact safely with staffed equipment and light vehicles using a combination of our advanced onboard perception system and proximity awareness.
“As the mining industry navigates the energy transition, Caterpillar recognizes that productivity and energy management are interconnected and can influence the total cost per ton. To tackle this, Caterpillar is continuously developing and integrating new MineStar capabilities to support battery-electric technology and charging solutions. These innovations will manage the coordination of energy and production across a mine site.
“The mine site of the future will be more complex than ever before as customers strive to meet the same production goals while balancing new challenges like energy management. We believe that the connection between automation and electrification will unlock the potential for a comprehensive ecosystem, integrating technologies to meet or exceed the demands of today and tomorrow.”
These technologies enable the trucks to maintain optimal following distances and safe operating speeds and, upon detecting an obstacle or anticipating an interaction, automatically stop or slow the truck’s speed.
Marc Cameron, senior vice president of Caterpillar Resource Industries, adds, “Of all the autonomous statistics and milestones Caterpillar has achieved over the past 11-plus years, the most important is that all of this has been reached without any reported injuries resulting from the mining trucks operating autonomously. We know that safety is of the utmost importance to our customers, and it is our top priority at Caterpillar as well.”
Cat MineStar Solutions impact the hauling operation in multiple ways – enabling fleet assignment, fully autonomous haulage, equipment tracking, production recording, material management, business insights, safety solutions, maintenance solutions and more. An optimized hauling strategy leveraging autonomy helps to support sustainable operations by moving more tons with fewer machines.
With retrofit kits available, today’s range of Cat mining trucks capable of fully autonomous operation span the 190- to 370- ton (210- to 410-ton) class sizes, including the Cat 789D, 793D, 793F and 797F, as well as the electric drive 794 AC and high-altitude 798 AC models. These models can be equipped with a portion of the autonomous kit from the factory, making them “Command-ready” to reduce installation time in the field.
Beyond haul trucks, the Cat 789D water truck platform can be equipped with Command for hauling, providing a fully autonomous solution to manage haul road dust. Additionally, Caterpillar now provides Command for hauling as a fully integrated factory offering on its 139-tonne (153-ton), Cat 785.
Commodities mined around the world using Command for hauling include iron ore, copper, gold, coal, oil sands, lithium, and traprock. The trucks face extremely challenging mining conditions, from the 40˚ C (104˚ F) heat and red dust in Western Australia to sub-freezing -40˚ C/F temperatures of the Canadian oil sands. They also operate in the deep pit copper mines of South America.
“We create software tailored specifically for each application, allowing trucks to efficiently navigate the axle-deep ruts of the oil sands or the steep grades of deep pit mines,” says Corey Wurtzenbacher[RZ1] , Vice President and General Manager of Technology and Global Sales Support. “Our engineers maintain close contact with mining customers and continuously improve software functionality, which is essential in the fast-paced technology sector to stay at the cutting edge with real-time advancements.”
Commanding reach
Autonomous trucks of the future will play a crucial role in the energy transition, as systems like MineStar Command and Fleet will be essential to managing the battery usage for battery-electric trucks. Planned new capabilities will play a role in helping mines manage power by monitoring and orchestrating the complex balance of onboard energy, available charging assets and production targets to achieve the lowest operating cost. “It’s critical that one system manages all the energy usages, so, in the future, we are not just managing ore but managing energy as well,” adds Wurtzenbacher.
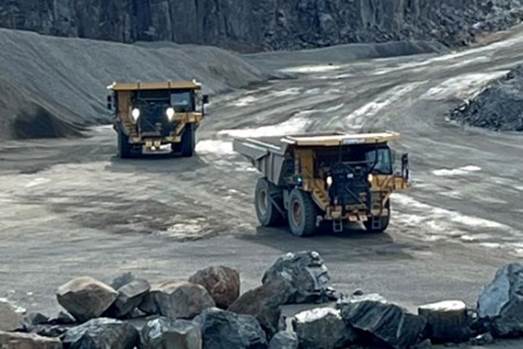
Caterpillar is also scaling into quarry applications, demonstrated by the company’s collaboration with Luck Stone to deploy Command for hauling at its Bull Run Plant in Chantilly, Virginia, USA. This is Caterpillar’s first autonomous deployment – technology, process, and people – in the aggregates industry and will expand the autonomous truck fleet to include the 90-tonne-class (100-ton-class) Cat 777.
“Instead of automating more than 100 trucks on a mine site that operates 24/7, we’re automating four trucks in a quarry that work 10 hours a day, so it’s not just about the technology,” says Johnson. “It is about how to transform our technology and processes to manage a smaller operation, so it makes money for the customer and does it safely. This can be a foundation for how we as a company move forward into autonomy in other industries.”
MineStar Solutions offers a range of remote and autonomous applications besides autonomous haulage to help further optimize mine site operations. This includes Command for drilling to automate the drilling operation, Command for dozing to enable remote dozer operation and Command for underground to enable remote operation of load-haul-dump (LHD) machines.
Cat® 785, 789 and 793 next generation trucks advanced features improve productivity and safety
The Caterpillar 125-to-240-ton (150 to 260 ton) productivity class mining trucks – Cat® 785, 789 and 793 next generation models – feature multiple new product developments. Next generation trucks are built on an advanced common platform with common electronic architecture, cab, and controls. “These next generation mining trucks feature a flexible technology platform and optional configurations to help each mining operation meet their goals,” says David Rea, vice president and general manager of Cat Rigid Frame Trucks, Bodies and Buckets.
All models are direct mechanical drive and boast the latest electronically controlled transmission with Advanced Power Electronic Control Strategy (APECS). The transmission offers smooth gear shifts for a smoother ride and delivers productivity and efficiency improvements. Forward momentum and torque are maintained while shifting with optimum gear selection resulting in faster acceleration.
There are more than thirty new or improved features with the next generation truck design, focusing on safety, productivity, and operator confidence. Truck development is focused on six key areas:
- Productivity-boosting cab
- Operator-focused environment that ergonomically accommodates a wider range of drivers
- Confidence-building controls that advance safety and operator confidence
- Innovative connectivity that offers increased data transfer speed, power of electronic control modules (ECMs) and advanced underlying architecture
- Improved maintenance
- Built for the future
Cat® Dynamic Energy Transfer system, the Cat® 798 AC mining truck
With its 372-tonne (410-ton) nominal rated payload, the Cat® 798 AC electric drive trucks deliver the highest standard payload available in its class size, higher speed on grade, easier maintenance and excellent resistance braking performance. The high-altitude arrangement (HAA) 798 AC features a 363-tonne (400-ton) payload, refreshed cab plus the latest performance, maintenance, and safety upgrades.
At MINExpo, the hardware was installed for the new Cat® Dynamic Energy Transfer system prototype which can be used to power the 798 AC’s electric drive system during operation. This fully Caterpillar-developed system is designed to transfer energy to both diesel electric and battery electric large mining trucks while they are working around a mine site. This allows it to charge a battery electric truck’s batteries while the machine is operating, improving operational efficiency and machine uptime.
Cat DET is comprised of a series of integrated elements, including a power module that converts energy from a mine site’s power source, an electrified rail system to transmit the energy and a machine system to transfer the energy to the truck’s powertrain. During the show, the 798 AC truck was positioned with the prototype onboard attachment arm connected to a 73-meter (240-foot) section of the Cat DET rail system.
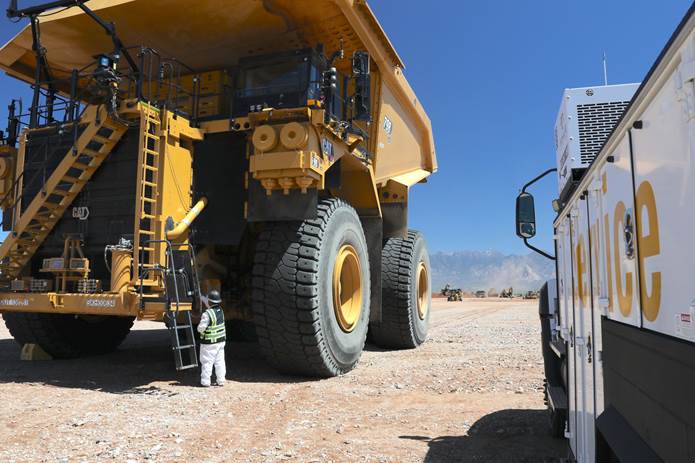
Features and performance
Standard Cat Payload Monitoring System technology delivers accuracy within 3%, with less sensitivity to load placement in the truck bed. Offering better accuracy with overload situations, it also reports carryback measurements to improve payload tracking. Consistent with other Cat mining trucks, the haul road management tool tracks and benchmarks haul road conditions to improve road maintenance and maximize truck lifecycle performance. The ability to correlate trend data to repair records and failure data helps to improve productivity, performance, and safety.
All high-altitude AC-drive mining trucks, like the exhibited 798 AC, can now be equipped from the factory Command ready to streamline integration of Command for hauling for future autonomous operation. The latest controller design improves data communication capability by increasing transfer rates through the serial port in Command mode. Monitoring of ton-kilometer per hour improves tire health monitoring for better tire management, especially at Command sites. An available health interface module (HIM) provides an interface for third-party collision avoidance/proximity detection, tire monitoring and driver safety systems.
Like all Cat mining trucks, the 798 AC now has braided harnesses and replaces p-clip fasteners with more rugged systems to improve durability. Monitored through onboard diagnostics, the integrated auto lube system improves greasing capability, enhances pump reliability, and prevents tank overfill and pressurization via auto shutoff. A ground-level reservoir provides easier access for inspection, refill, and maintenance. Also available, the solid bar rock ejector improves performance in demanding applications where chain rock ejectors are less effective.
Reducing emissions
The diesel-electric design of the 798 AC, as well as all Cat AC-drive trucks, delivers high payload, fast speeds, and excellent acceleration, so miners get the most from the fuel burned. Equipping the truck with DET to make use of electric power on certain sections of the haul road provides opportunities to reduce fuel burn even more. To optimize fuel consumption at the mine site, the 798 AC offers a range of engine power options from 2,050 to 3095 kW (2,750 to 4,150 hp). Engines are compatible with diesel blended with lower-carbon intensity fuels like biofuels and renewable fuels, as well as blends with synthetic fuels.
“Caterpillar and Cat dealers provide a variety of tools to assist miners in achieving their emissions-reduction goals. These tools include scale studies designed to optimize empty machine weight, minimize carryback, and ensure maximum payload. Site assessments examine multiple aspects of the mine site to enhance haul road efficiency, resulting in faster cycle times, improved productivity, reduced maintenance costs, and lower fuel consumption per cycle. Additionally, Cat Reman and Cat Rebuild programs help preserve raw materials, conserve energy, and reduce emissions.”
Komatsu: Continuity, Efficiency …and impressive results.
When it comes to mining machines hauling their unimaginable loads Komatsu are also one of the leaders within this great industry of ours.
For more than a century the company has been creating value for its customers through manufacturing and technological innovation, partnering with others to empower a sustainable future where people, business and the planet thrive together. Every aspect of their truck manufacturing capability is rigorously engineered to help reduce cost per tonne. From multiple innovative fuel saving features to industry-leading build quality and longevity, Komatsu offer a super-sized range of truck hauling capacities.
The technological advancements showcased at recent international exhibitions were impressive, and I appreciated the opportunity to reach out and engage with the Komatsu team.
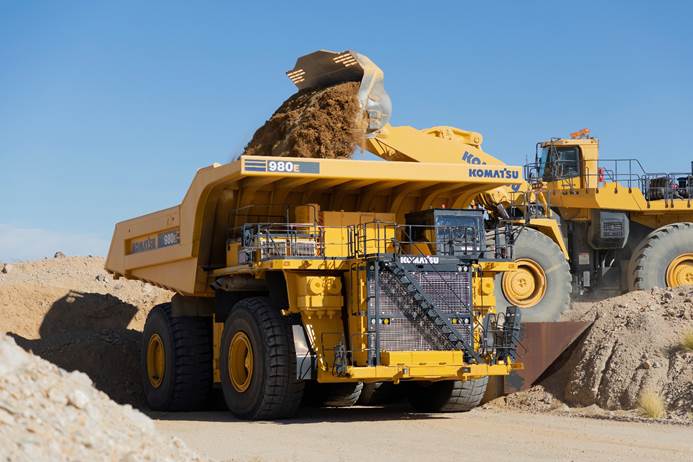
MQW: Questions
- MQW: How does Komatsu integrate new technologies to improve fleet management?
- A: At Komatsu, we leverage decades of experience optimizing mining operations to help our customers increase productivity, improve efficiencies, and reduce operating costs. Whether a mine aims to move more material with its existing fleet or achieve cost savings through operational enhancements, our fleet management technologies provide intelligent solutions tailored to those needs. Our industry-leading solutions, including DISPATCH Fleet Management System (FMS) and Frontrunner Autonomous Haulage System (AHS), offer real-time optimization of loading and hauling operations, ensuring efficient dispatching and decision-making at every stage. Komatsu’s autonomous haulage technology, coupled with the reliability and durability of our electric drive trucks, has helped mines worldwide improve productivity while reducing the total cost of ownership, delivering cost savings and promoting zero harm through safer, more consistent operations.
- We recognize that a truly optimized fleet extends beyond individual truck performance to the entire mining operation. Our open supervisory platform allows customers to manage mixed fleets by integrating with various systems and equipment across mine site operations. Using Wi-Fi and LTE connectivity, real-time data from onboard health and performance monitoring helps drive predictive maintenance strategies, ensuring truck servicing is based on actual conditions rather than fixed-hour intervals. Additionally, our mining technology solutions team works closely with customers to integrate and implement these technologies, analyze data, and drive optimization across all tools within the platform. As a leader in autonomous haulage, Komatsu has commissioned over 815 autonomous haul trucks across more than 20 sites in five countries, setting the standard for efficiency, safety, and productivity in modern mining.
- MQW: How are Komatsu trucks evolving to take into account challenging and remote environments?
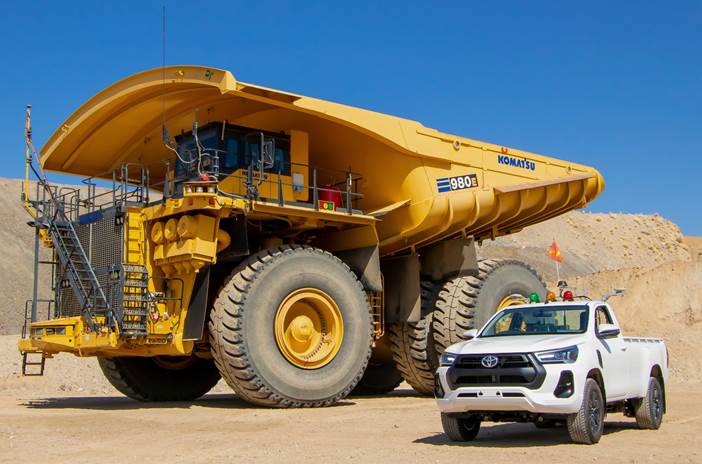
- A: As mining operations push further into remote and challenging environments, equipment must evolve to withstand extreme conditions while maintaining efficiency and reliability. Komatsu collaborates closely with customers to anticipate these challenges and develop solutions tailored to their specific needs. Whether it’s increasing payload capacity, optimizing engine performance for high altitudes, or equipping trucks with cold-weather kits, we take an application-engineering approach to ensure our machines are optimized for the conditions in which they operate.
- Our engineering process follows a continuous improvement methodology—Plan, Do, Check, Act (PDCA)—to ensure that our equipment is not only designed to meet initial specifications but is also continually assessed for real-world performance. This iterative approach allows us to work alongside customers over time, making necessary adjustments based on operating data and feedback. Our truck designs consider key factors such as haul distance, lift, ground conditions, and material abrasiveness, ensuring that mining operations in even the harshest environments can maximize efficiency and uptime. By remaining flexible and adaptive, Komatsu provides the performance and reliability mining companies need to operate successfully in these evolving conditions.
- MQW: There is a growing trend of partnerships between mining companies and truck manufacturers to develop customized, efficient, and tailored solutions. Who is Komatsu partnering with and are there any case studies of how this has developed over time?
- A: At Komatsu, we recognize that meeting the evolving demands of the mining industry requires collaboration with strategic partners who bring specialized expertise to the table. For example, in the development of trolley-assist systems, we focus on building reliable haul trucks and electric drive motors, while partners such as ABB and Siemens contribute their expertise in designing and optimizing trolley lines, electrical substations, and power distribution systems. By working together, we ensure that the full trolley-assist solution maximizes productivity, reduces fuel consumption, and lowers carbon emissions, helping mines achieve their sustainability goals while improving operational efficiency.
- In the pursuit of alternative energy solutions, Komatsu is collaborating with General Motors to develop hydrogen fuel cell technology, positioning us at the forefront of power transformation in mining. Our Power Agnostic Drive Train (PADT) platform is designed to accommodate future energy sources, allowing for seamless integration of new power technologies as they become viable replacements for traditional mechanical drives. Additionally, our long-standing partnership with Cummins continues to drive innovations in high-altitude engine performance, ensuring that our trucks can deliver the necessary horsepower in oxygen-limited environments.
As the mining industry evolves, Komatsu remains committed to embracing new technologies and working with partners to develop the most efficient, sustainable, and adaptable solutions for our customers. These partnerships enable us to stay ahead of industry shifts and deliver mining trucks that meet the challenges of today while preparing for the demands of tomorrow.
Liebherr: Innovative Technology, Commitment to Excellence and a shared vision.
Recent exhibitions showcased impressive technological advancements, notably Liebherr’s Haul Trucks, which represent years of dedication toward achieving zero-emission goals. Among several announcements was the unveiling of their autonomous, battery-electric T 264 Haul Truck. Developed in partnership with Fortescue, this truck demonstrates Liebherr’s experience in developing, manufacturing, and providing innovative solutions for the mining industry. This article will examine how Liebherr is establishing itself as a leading global mining equipment partner.
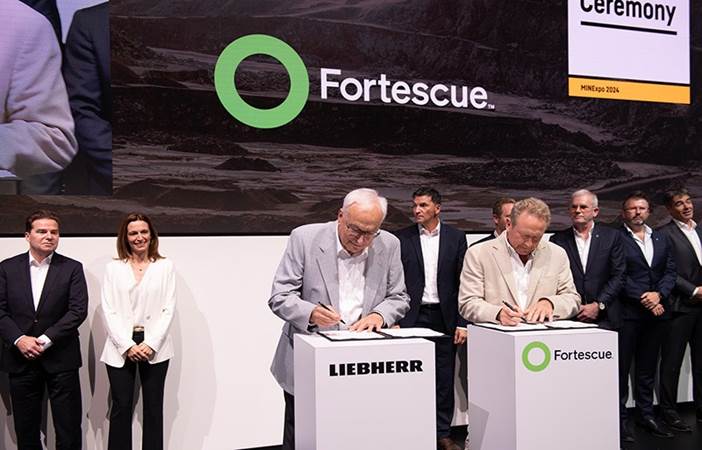
It is the single largest equipment deal in the Liebherr Group’s entire 75-year history.
The partnership includes jointly developed technology that paves the way for carbon-free mining and features a total of 475 zero emission Liebherr machines – approximately 360 autonomous battery-electric trucks, presented to the industry at an exciting event at MINExpo: fifty-five electric excavators and sixty battery-powered dozers.
As part of the deal, Liebherr and Fortescue will deploy a complete autonomous battery-electric haulage solution for large scale mining operations.
A zero-emission battery power system used in the battery-electric trucks has been developed by Fortescue Zero, Fortescue’s technology arm.
Fortescue Zero’s battery power system will also be integrated into an electric version of Liebherr’s flagship mining dozer, the PR 776.
The large scale zero emission mining ecosystem developed by Liebherr and Fortescue will be available to the rest of the mining industry in the near future.
This deal is expected to create one of the world’s largest zero emission mining fleets and represents a major breakthrough in the pursuit of a mining industry no longer reliant on fossil fuels.
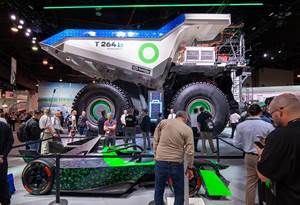
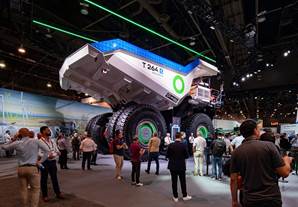
During an impressive event at MINExpo in Las Vegas, USA, Liebherr and Fortescue announced a significant expansion of their partnership and unveiled the jointly developed autonomous battery-electric T 264 truck. Both Dr Andrew Forrest and Dr Willi Liebherr attended the event to celebrate the historic deal. Together, the two companies will develop and validate a range of zero emission mining solutions, which will result in the supply of 475 new Liebherr machines featuring Fortescue’s innovative green technology to Fortescue’s operations in Western Australia. This represents about two thirds of the current mining fleet at Fortescue’s operations. Fortescue’s mining fleet consumed approximately four hundred million litres of diesel in FY24 and accounted for 51 per cent of its Scope 1 emissions. Liebherr and Fortescue are committed to having a comprehensive and large scale zero emission mining ecosystem operational by 2030. Both companies have confirmed that, through their continued cooperation, customers will be able to access this ecosystem for their own operations in the coming years. The deal, with all the equipment and technological innovations, amounts to the single largest deal made in the Liebherr Group’s 75-year history.
Liebherr-Components: excellence at the heart of mining machines
Liebherr’s components product segment presents innovative technologies that are at the core of every powerful mining machine. Liebherr’s commitment to excellence and decarbonization can be seen in every product manufactured – be it a hydrogen engine, a travel, or a wheel drive, a CFRP hybrid hydraulic cylinder, an advanced slewing bearing with bearing clearance monitoring or the Reman program. Further, Liebherr offers exchange components for the mining aftermarket, providing customers with a comprehensive service they can profit from.
Liebherr as a component manufacturer.
When manufacturing mining machines, Liebherr’s priority is to design matching components to withstand the highest loads and most challenging conditions in mines over a long operation time. Liebherr’s vast expertise in the development and manufacturing of powertrain technology brings clear advantages – from reliable components at the heart of reliable machines to continuous powertrain development based on the results of field tests.
Recently, Liebherr has begun to integrate its own series of engines into its excavators and trucks in new markets all over the world at first fit or as repowering projects.
‘As a part of its international strategy, Liebherr equips its machine fleets with its own high-performance components. In this way, Liebherr guarantees that the entire machine meets the most stringent standards in terms of safety, performance, and reliability,’ says Steffen Apel, key account manager, combustion engines for the mining industry, Liebherr-Components AG.
To master one of the significant challenges of this generation – the reduction of global greenhouse gases – Liebherr is working on alternative powertrain concepts. For example, Liebherr’s components product segment is developing ammonia internal combustion engine technology. The latter can be used in mine operations, where electrification is either not possible or not economical. Ammonia offers several advantages such as high energy density, ease of transportation and excellent storage capacity.
Liebherr also transforms used components into new parts in accordance with industry standards through its Reman program, contributing to the preservation of important resources. ‘Up to 75 % of raw materials and energy can be saved through the remanufacturing of used components. The carbon footprint can also be reduced by over 50 %,’ adds Jens-Christian Wannenwetsch, managing director, Liebherr-Ettlingen GmbH. Moreover, the remanufacturing of used parts cuts material costs, reduces downtime, and increases the availability of equipment. The Liebherr Group is currently remanufacturing used components at around fifteen locations with a total of 550 employees worldwide. Each year, approximately 7,500 components and countless individual parts are given a second life. Most of these locations are operated by Liebherr’s mining product segment, with a smaller portion belonging to the component’s product segment. A regular exchange of experience between these product segments ensures a continuous process improvement.
To increase efficiency, Liebherr uses both lightweight design and fibre composite technology (CFRP) for the manufacturing of a wide range of products. ‘Our manufacturing approach brings with it the significant advantage of component properties comparable or superior to those of steel, alongside weight reduction. When applied in mining, the latter allows the use of larger attachments for mining excavators, which increases digging performance, operational efficiency and reduces emissions as a side benefit,’ says Dominic Gottwald, team leader composites technology, Liebherr-Components Kirchdorf GmbH. ‘Liebherr is well-known for its quality management processes, which also apply to CFRP hybrid hydraulic cylinders.’
BHP and Liebherr sign new Global Framework Agreement
In 2024 one of the largest mining events in the world took place in the USA, Liebherr and BHP announced the signing of a Global Framework Agreement. Built on an existing agreement, this renewed partnership solidifies Liebherr as one of BHP’s preferred mining equipment suppliers across the company’s global assets, strengthening their collaborative efforts with the aim of advancing operational innovation and reducing greenhouse gas emissions across BHP’s global operations.
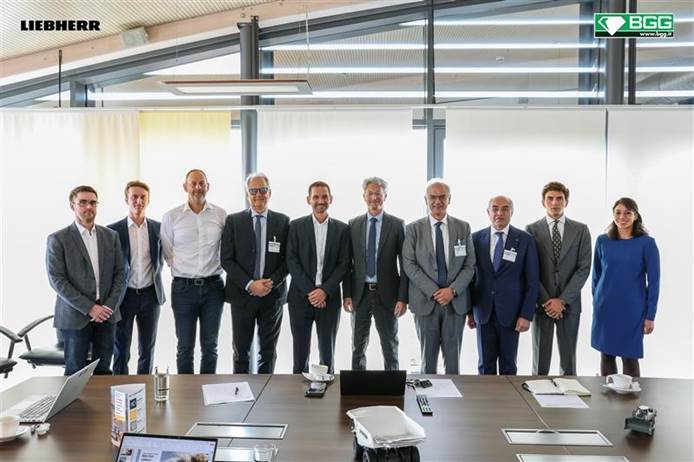
Liebherr, a world leader in mining equipment innovation, and BHP, one of the world’s foremost resources companies, have announced a Global Framework Agreement (GFA). This agreement further cements the long-standing partnership, uniting both companies in their shared pursuit of innovative mining solutions.
Building on a history of successful collaboration, the GFA merges BHP’s drive for responsible resource extraction with Liebherr’s technological expertise in heavy machinery. Together, they aim to continue pushing the boundaries of operational efficiency while enabling greenhouse gas emission reductions for BHP’s operations.
‘This extension is a testament to the strength of Liebherr’s relationship with BHP and our shared vision for the future of mining,’ says Dr Jörg Lukowski, executive vice president, sales and marketing, Liebherr-Mining Equipment SAS. ‘Over the years, we have worked closely with BHP to develop solutions that not only improve operational efficiency but also drive more sustainable outcomes. We are excited to continue this journey and deliver the latest advancements in automation, digitalisation, and electrification to their operations globally.’ Under this agreement, Liebherr and BHP will collaborate closely on delivering world-class machine performance and integrating the latest advancements in safety, automation, digitalisation, and electrification across BHP’s global mining operations.
Partner for success
The partnership between Liebherr and BHP, which spans more than two decades, has seen the deployment of Liebherr ultra-class excavators across BHP’s global assets, including R 9600 Generation 8 machines. Notably, BHP’s flagship South Flank iron ore operation in the Pilbara region of Western Australia received its first R 9600 in March 2020. In early 2024, BHP took delivery of its first electric excavator at its Yandi mine – a Liebherr R 9400 E. This machine is a fully electric version of the R 9400.
BHP’s chief commercial officer, Ragnar Udd, says, ‘This renewed agreement between BHP and Liebherr not only reaffirms our trusted partnership over the years but also signals our collective ambition towards helping to influence the future of mining through innovation, safety, productivity, operational excellence and greater sustainability.’
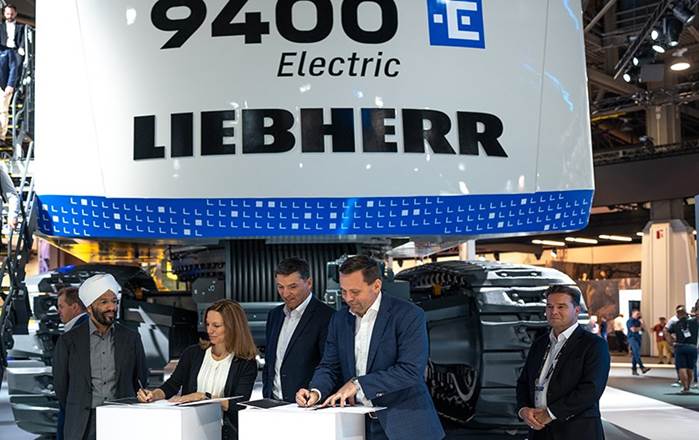